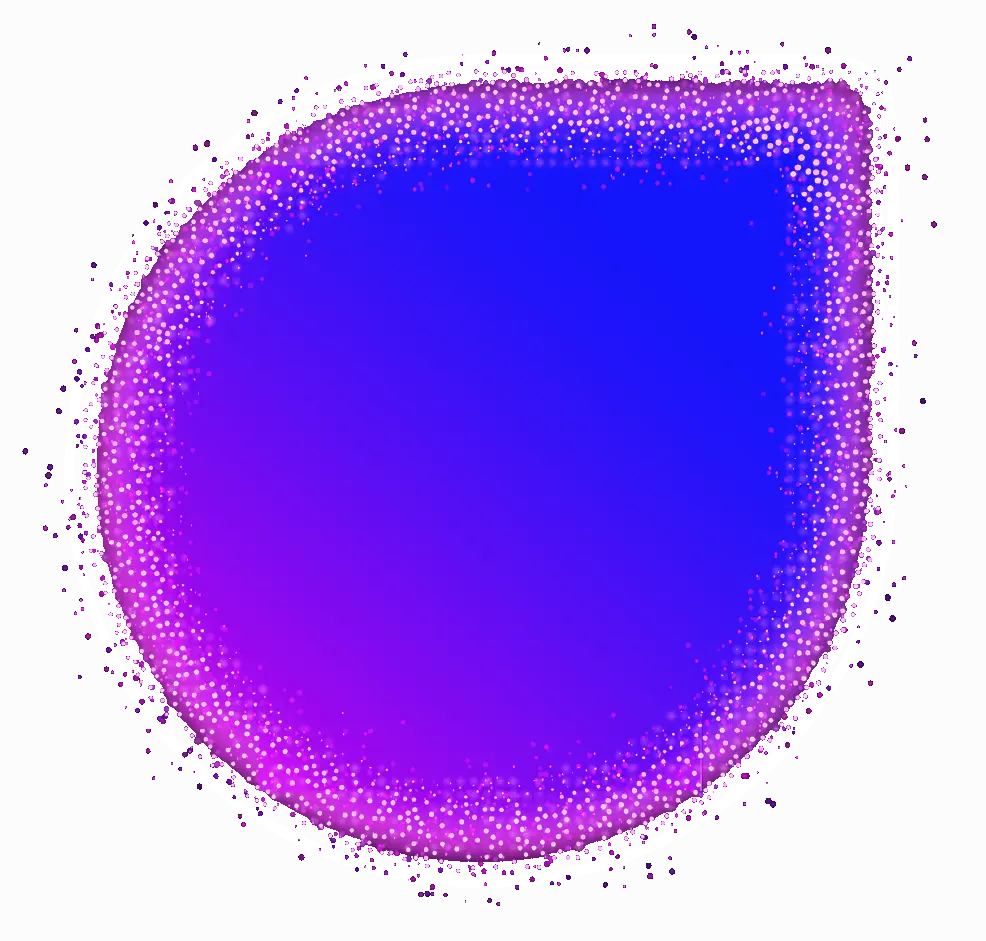

Secure, Seamless, Sterile
Track and connect critical instrument and tray data across their entire SSD lifecyle for a safer, more efficient, and transparent workflow.
Book a consultation:
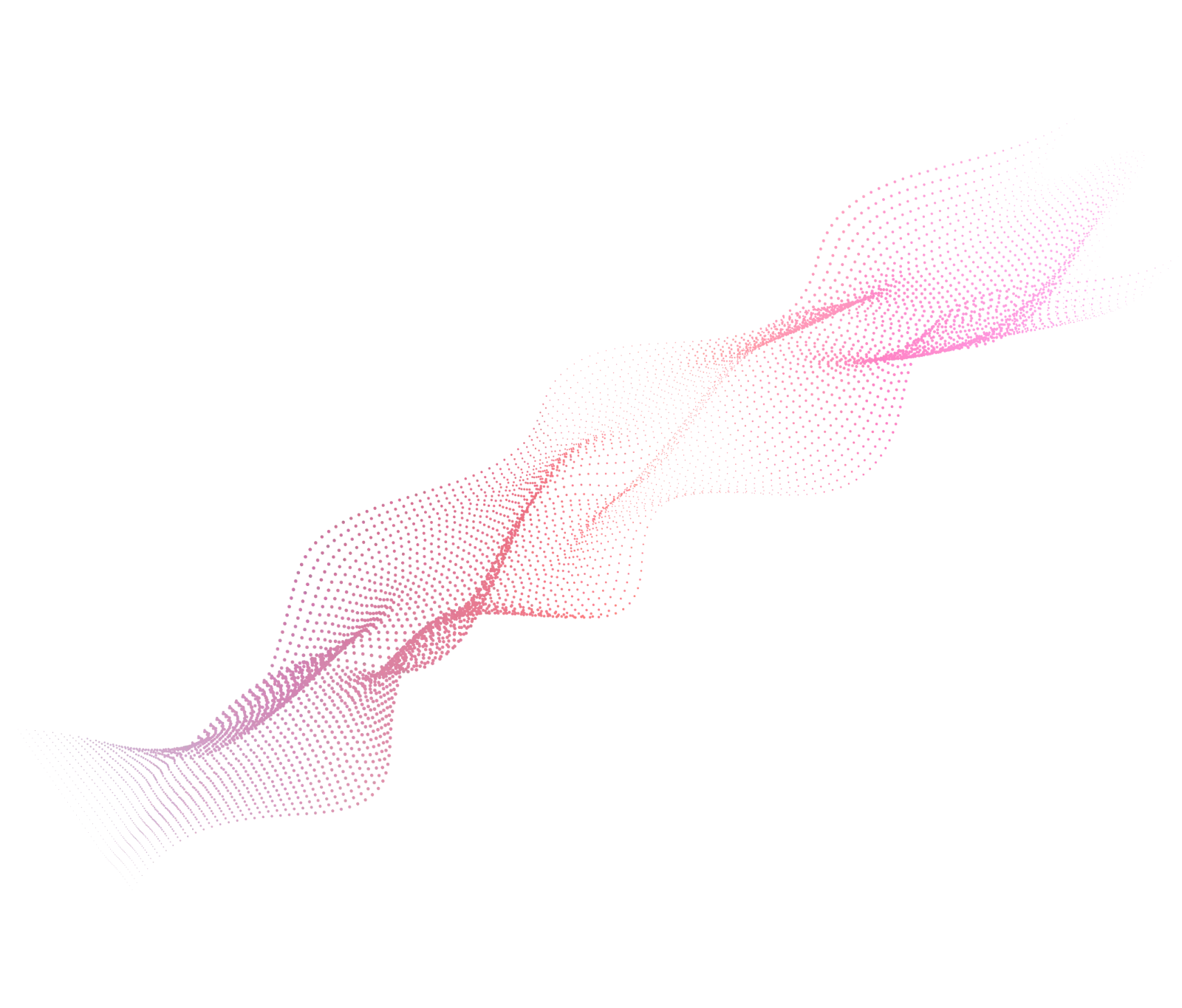
Trusted by:
What they say:
The Big Picture Perspective You Need:
- Gain a 360°, live view of the shop floor, tracking every tray at every workflow step
- Halve turnaround with actionable optimisations so you can increase workload, all while improving staff satisfaction
- Gain a forward-looking, predictive perspective, so you can get trays to theatres ahead of time
- Ensure every station performs compliantly, with everything securely accounted for thanks to digital checkpoints
Flexible and Forward-Looking
Track every stage of your instrument’s journey—from entering SSD to when it next needs to be used—with an intelligent, automated solution designed to connect your workflow data, enhance patient safety, and protect your staff.
How it Works:
Manual Wash
Document every detail—sink IDs, solution temperatures, and consumables like brushes and irrigation methods:
- Tray ID
- Sink ID
- Water temperature
- Solution rate and type
- Brushes used, type, and manufacturer ID
- Irrigation method and associated details (i.e. syringe batch details)
- Buttons wash
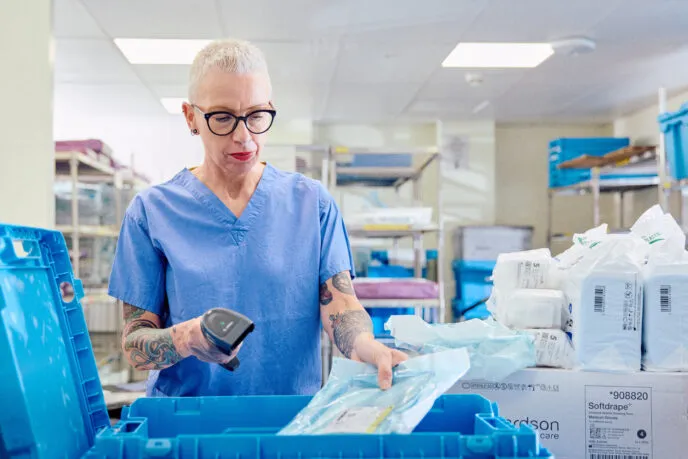
Machine Wash
Interface directly with machines for real-time monitoring and compliance checks:
- Verify compliant washes through washer interfacing
- Upload washer reports into ScopeTrack software
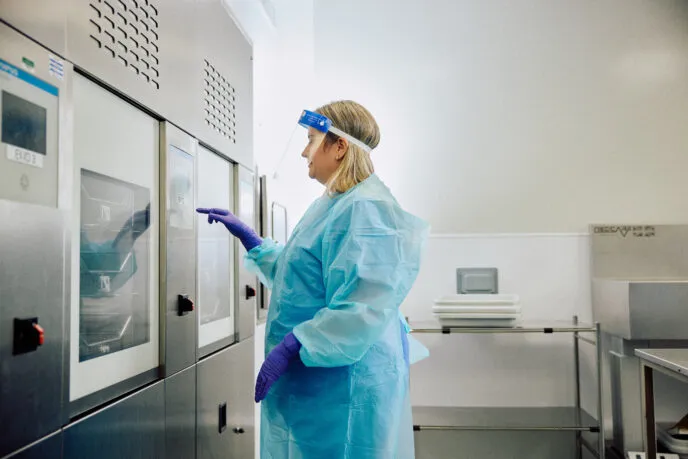
Drying and Storage
Track cabinet times, drying stages, and storage limits, with configurable settings for different cabinet types:
- Hook ID
- Drawer ID
- Set up custom time restraints dependent on cabinet type requirements (i.e. minimum dry times)
- Offsite sterilisation tracking
- Part association tracking
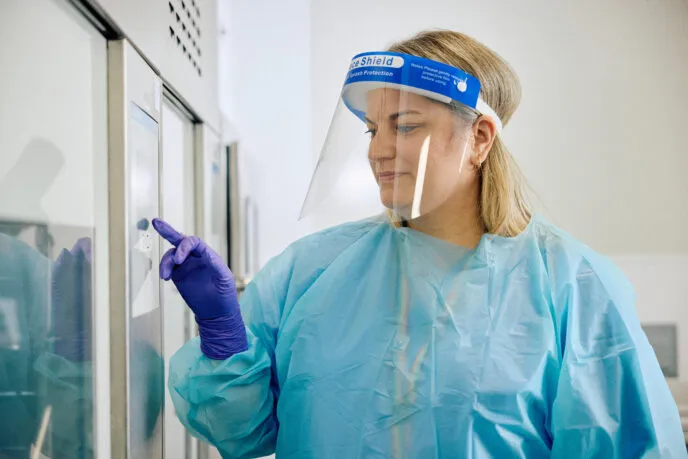
Dispatch into Theatres
Ensure trays are ready for use with streamlined label generation and transport tracking:
- Labels are produced when the tray is ready for use
- Trolley cleaning process tracking
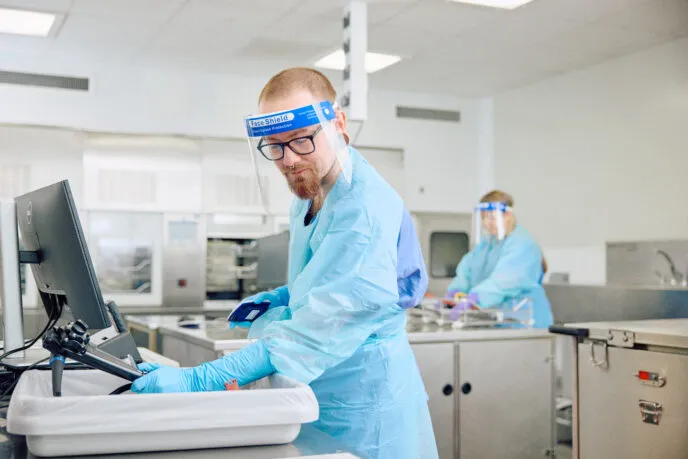
There’s Power in Precision
Documentation:
Easily attach documents and images to a tray at any stage of the decontamination process. Assign key files and information—such as decontamination protocols, theatre details, technical specifications, and comments—ensuring each tray and instrument is paired with the precise process it requires.
Repairs:
Identify repairs or instruments needing quarantine and ensure a spare is always available in cases of emergency
Alerts:
Get tailored alerts for certain processes, expiry or service check dates, current status (in cabinets or machines) and number of cycles. Choose when you’d like to be alerted.
Reports:
Build your own reporting templates that can interface into clinical systems.