Athera FingerPrint
Why Flexibility is Integral to Traceability Systems: A Royal United Hospital Case Study
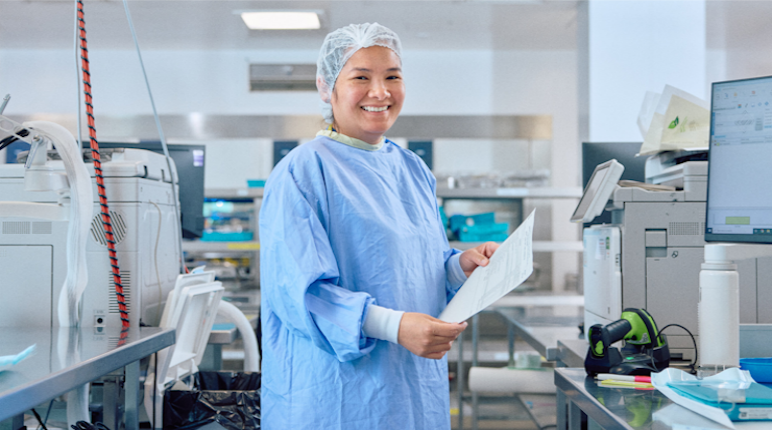
Royal United Hospitals Bath NHS Foundation Trust (RUH) has had a long-standing partnership with Athera Healthcare’s advanced instrument traceability and management system, Athera FingerPrint. However, before finding FingerPrint, the hospital faced rigid systems, a lack of flexibility from providers, and an unclear pathway to progression.
The Challenge:
As the SSD department faced increasing traceability demands, especially with more complex instruments such as endoscopy, they required a solution that offered full flexibility, comprehensive reporting capabilities, and seamless integration with their existing infrastructure.
RUH had previously relied on various alternative traceability systems but found these solutions too rigid as they were expected to adapt to the solution, rather than have the solution adapt to them. “We wanted less of a ‘this is the way you should be working’ and more of a ‘we flex to suit you’ – which is exactly what FingerPrint offered” adds Soby, Head of Sterile Services & Trust Decontamination Manager. This flexibility was crucial for the hospital, which needed a system that could evolve alongside their changing needs and integrate with their new equipment.
“We haven't had a surgery cancellation due to inefficiencies within SSD for 3/4 years now... thanks to process improvements built from FingerPrint’s tech.”
Soby Joseph
Head of Sterile Services & Trust Decontamination ManagerRoyal United Hospitals Bath NHS Foundation Trust
“We wanted less of a ‘this is the way you should be working’ and more of a ‘we flex to suit you’ - which is exactly what FingerPrint offered”
Soby Joseph
Head of Sterile Services & Trust Decontamination ManagerRoyal United Hospitals Bath NHS Foundation Trust
Before switching to Athera FingerPrint, Royal United Hospital grappled with several challenges:
- Lack of flexibility: other solutions were rigid, forcing the hospital to adapt their internal processes to fit the software rather than the other way around. The inflexible nature of these systems, coupled with unclear pricing that was continually escalated as additional (but necessary) add-ons were uncovered, created a difficulty to progress
- Traceability gaps: with a growing focus on patient safety and compliance, they needed to extend traceability beyond reusable surgical instrument reprocessing, covering all products, including high-level disinfection and decontamination procedures
- Outdated training and reporting: both training and reporting were paper-based, leading to inefficiencies, potential for human error, and high paper usage. The manual nature of these processes made it difficult to maintain accurate records, leading to delays and a lack of real-time insights into operations
The solution: a tailored and integrated approach with Athera FingerPrint
The search for a flexible traceability solution led them to Athera FingerPrint, which stood out for its adaptability and ability to integrate seamlessly with the department’s existing processes.
We haven’t had a surgery cancellation due to inefficiencies within SSD for 3/4 years now” says Soby Joseph, Head of Sterile Services & Trust Decontamination Manager “because the SSD team knows exactly what’s happening now thanks to process improvements built from FingerPrint’s tech
FingerPrint is a lot more ‘colourful’ than other solutions. It has more functionality which has had a massive impact on efficiency.
The Athera FingerPrint Impact:
Preventative Maintenance
“This feature has been invaluable,” says Soby. “Previously, we had to manually track the usage of each tray, which was prone to human error. Now, FingerPrint will tell us that this particular tray that has been used 40 times needs to go to maintenance after 2 more uses, for example.”
“This not only extends the lifespan of our instruments but also enhances patient safety.” adds Soby.
Loanset Management
Unfamiliar instruments from loanset providers have always been a challenge, not just for RUH, but for Trusts across the UK. The complexity of gauging new equipment protocols and the time it takes to learn these protocols often cause delays in the cleaning process. “When we get new instrument sets we review the manufacturer’s instructions for cleaning and assembling and they can be really challenging to learn” says Beverley Parmenter, Decontamination Quality & Resourcing Manager. With FingerPrint, however, the process has become much more manageable: “we’re able to set up tracker alerts for each phase of assembling and cleaning, providing detailed guidelines for staff to follow.”
FingerPrint’s capacity for setting up tailored alerts and embedded multimedia support guide staff through each phase of the cleaning and assembly process, ensuring that everything is done correctly the first time. This not only reduces the likelihood of mistakes but also speeds up the entire process, allowing the hospital to meet tight deadlines, without compromising quality.
Athera FingerPrint helps not only extend the lifespan of our instruments but also enhance patient safety.
Training Aid
Training new staff on the innumerable number of instruments is no small feat, but FingerPrint’s multimedia functionalities have enabled staff training process improvements.
The system’s ability to seamlessly integrate multimedia elements, such as documents and images, allows staff to directly access and distribute training materials both on-screen and in printed form. This capability ensures that washroom and packing teams receive comprehensive resources, making complex procedures easier to understand and follow.
The ability to add labeled images of instruments directly into the training materials has been a game-changer. This visual aid helps staff quickly identify instruments, ensuring that they can carry out their tasks accurately and efficiently. “It’s the way of the future,” says Beverley. “Having everything digitised and easily accessible helps us get things 100% right more often, which is critical in a high-stakes environment like ours, particularly when we’re working with more complex surgical equipment including Robotics.”
Equality and Diversity
On a more personal scale, a member of the SSD team mentioned how FingerPrint helps with his dsylexia: “As someone with dyslexia, having a digital solution makes the world of difference. With FingerPrint, I can press ‘Shift 5’ to use the search shortcut, type a part of the word in and find that instrument directly.”
Royal United Hospital places great emphasis on inclusivity, running projects such as Project SEARCH, which Beverley expresses they are incredibly proud of. Project SEARCH exists to challenge traditional views on employing people with learning difficulties; giving opportunities to people who are oftentimes overlooked. Now, RUH has employed 40 interns as full-time, paid staff as well as eight others in part-time and bank positions. You can read more about Project SEARCH here.
Sustainability
Beverley also explains how RUH is committed to reducing its environmental impact: “we are the second highest paper user in the hospital, printing in excess of 50k papers a month, processing 20k trays a month”. The SSD team are now working with the FingerPrint team to continue to cut down their paper wastage, aligning with the hospital’s sustainability goals.
Closing remarks:
“Traceability is integral to our business” reaffirms Soby. As Royal United Hospital’s SSD department continue to evolve as they introduce new process pathways, new instrument types, and new technologies, FingerPrint will seamlessly integrate and support every step.
And whilst the SSD team enjoys the benefits that full traceability, instrument management, and reporting can provide, a critical next step is extending this visibility beyond the Sterile Services Department and into the surgery theatres, store-rooms, and other key areas.
“The SSD get calls from theatres asking for kit which SSD had sent 3 days prior!” states Dave Lockyer, Deputy Decontamination Manager
With cross-department traceability, instrument management can be a game-changer – reducing waiting lists, preventing no-go surgeries, and enhancing the overall hospital strategy.
Traceability is integral to our business
Looking ahead, Athera Healthcare’s focus is on bridging this gap. By expanding FingerPrint’s traceability capabilities to cover the entire lifecycle of surgical instruments—from sterilisation to the operating room—the hospital can ensure that every department has real-time access to the equipment they need. This will not only streamline operations but also enhance patient care.
Book a Demo
Arrange a one-to-one demonstration with a member of our dedicated team. We collaborate to tailor the experience so you can see how our solutions can be applied in your specific context and utilised effectively to achieve your objectives.